Destylator przemysłowy to urządzenie, które odgrywa kluczową rolę w wielu procesach produkcyjnych, szczególnie w przemyśle chemicznym, petrochemicznym oraz spożywczym. Jego głównym zadaniem jest oddzielanie składników mieszanin na podstawie różnicy w temperaturze wrzenia. Proces ten polega na podgrzewaniu cieczy, co prowadzi do parowania jej składników, a następnie skraplaniu pary w celu odzyskania czystych substancji. W przemyśle chemicznym destylatory są wykorzystywane do oczyszczania i separacji różnych związków chemicznych, co pozwala na uzyskanie wysokiej czystości produktów końcowych. W branży spożywczej destylatory są używane do produkcji alkoholu oraz ekstraktów aromatycznych.
Rodzaje destylatorów przemysłowych i ich charakterystyka
W przemyśle istnieje wiele rodzajów destylatorów przemysłowych, które różnią się konstrukcją oraz zastosowaniem. Najpopularniejsze z nich to destylatory prostokątne, kolumnowe oraz próżniowe. Destylatory prostokątne charakteryzują się prostą budową i są często stosowane w mniejszych zakładach produkcyjnych. Z kolei destylatory kolumnowe są bardziej skomplikowane i umożliwiają przeprowadzanie bardziej zaawansowanych procesów separacji. Dzięki zastosowaniu kolumny z różnymi poziomami, możliwe jest uzyskanie wyższej czystości produktów. Destylatory próżniowe działają w obniżonym ciśnieniu, co pozwala na destylację substancji o wysokiej temperaturze wrzenia bez ryzyka ich rozkładu.
Jakie są kluczowe elementy konstrukcyjne destylatora przemysłowego
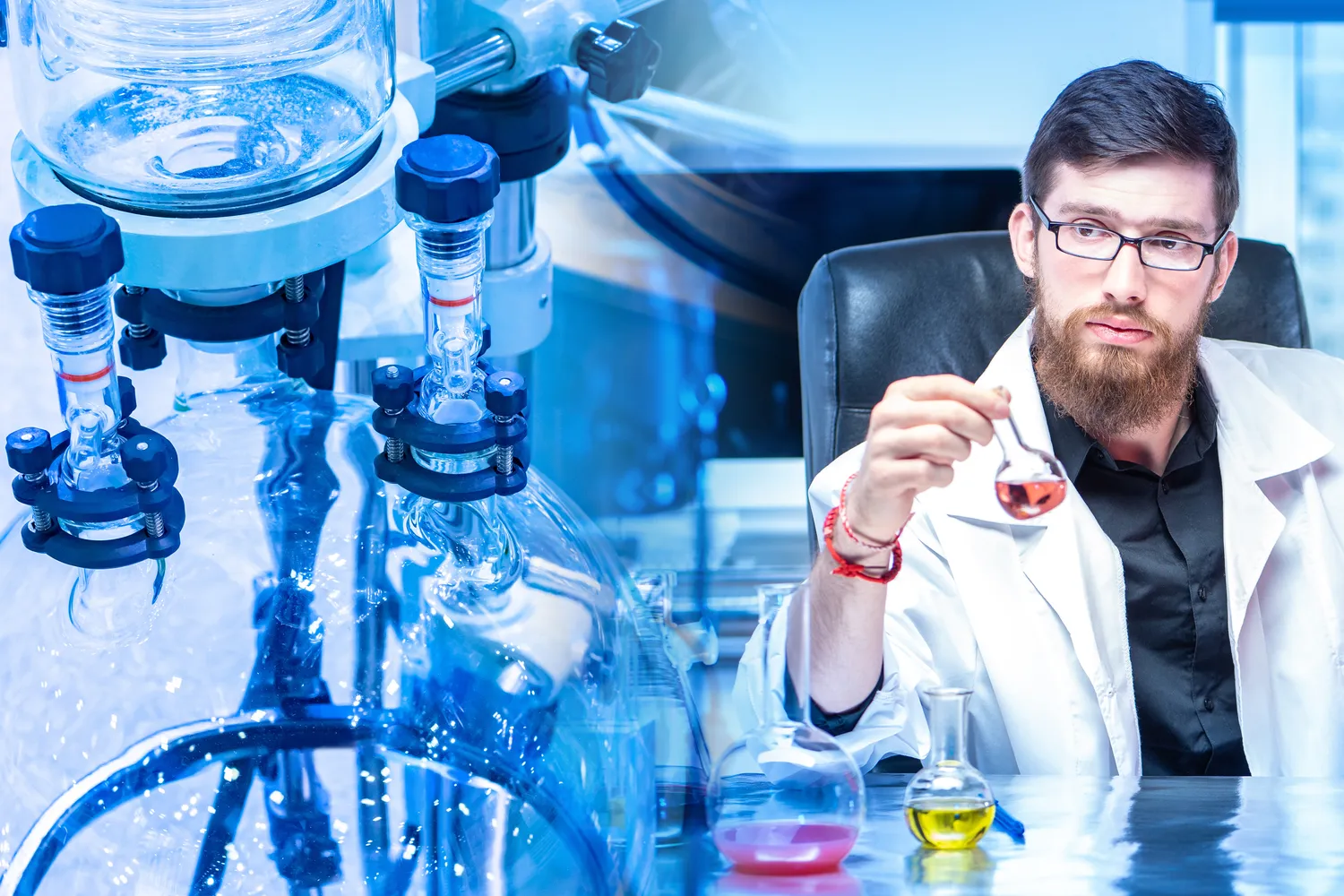
Kluczowe elementy konstrukcyjne destylatora przemysłowego obejmują zbiornik do podgrzewania cieczy, kolumnę destylacyjną oraz system chłodzenia. Zbiornik jest miejscem, gdzie odbywa się podgrzewanie surowca do odpowiedniej temperatury, co umożliwia parowanie składników. Kolumna destylacyjna to istotny element procesu separacji, który pozwala na wielokrotne skraplanie i parowanie substancji, co zwiększa efektywność procesu. System chłodzenia jest niezbędny do skraplania pary powracającej z kolumny do postaci cieczy. Dodatkowo w nowoczesnych destylatorach często stosuje się różnego rodzaju czujniki i automatyczne systemy sterowania, które monitorują parametry procesu i zapewniają optymalne warunki pracy.
Jakie są korzyści z używania destylatora przemysłowego
Używanie destylatora przemysłowego niesie ze sobą wiele korzyści dla przedsiębiorstw zajmujących się produkcją chemiczną czy spożywczą. Przede wszystkim pozwala na uzyskanie wysokiej czystości produktów końcowych, co jest kluczowe w wielu branżach, gdzie jakość ma ogromne znaczenie. Destylacja umożliwia także efektywne odzyskiwanie surowców z odpadów produkcyjnych, co przyczynia się do zmniejszenia kosztów operacyjnych oraz wpływu na środowisko. Dodatkowo nowoczesne destylatory charakteryzują się dużą wydajnością energetyczną, co pozwala na oszczędności w zużyciu energii podczas procesów produkcyjnych. Warto również zauważyć, że automatyzacja procesów związanych z destylacją zwiększa bezpieczeństwo pracy oraz minimalizuje ryzyko błędów ludzkich.
Jakie są najczęstsze problemy z destylatorami przemysłowymi
Destylatory przemysłowe, mimo swojej zaawansowanej technologii, mogą napotykać różne problemy, które wpływają na ich wydajność i jakość produktów. Jednym z najczęstszych problemów jest zatykanie kolumny destylacyjnej, co może prowadzić do obniżenia efektywności procesu separacji. Zatykanie może być spowodowane osadzaniem się zanieczyszczeń lub nieodpowiednich składników w procesie. Innym istotnym problemem jest niewłaściwe ustawienie temperatury, co może prowadzić do niepełnej destylacji i uzyskania produktów o niskiej czystości. W przypadku destylatorów próżniowych, utrzymanie odpowiedniego ciśnienia jest kluczowe; jego wahania mogą wpływać na wyniki procesu. Problemy z systemem chłodzenia również mogą wpłynąć na skuteczność destylacji, ponieważ niewłaściwe skraplanie pary prowadzi do strat surowców.
Jakie są koszty związane z zakupem destylatora przemysłowego
Koszty zakupu destylatora przemysłowego mogą znacznie się różnić w zależności od jego typu, rozmiaru oraz zastosowania. Na rynku dostępne są zarówno małe jednostki przeznaczone dla mniejszych zakładów produkcyjnych, jak i duże systemy stosowane w przemyśle chemicznym czy petrochemicznym. Ceny prostych destylatorów mogą zaczynać się od kilku tysięcy złotych, podczas gdy bardziej zaawansowane modele mogą kosztować setki tysięcy złotych. Dodatkowo należy uwzględnić koszty związane z instalacją oraz uruchomieniem urządzenia, które również mogą być znaczące. Koszty eksploatacyjne, takie jak zużycie energii, konserwacja oraz ewentualne naprawy, także powinny być brane pod uwagę przy planowaniu budżetu na zakup destylatora.
Jakie są innowacje technologiczne w dziedzinie destylacji przemysłowej
W ostatnich latach branża destylacji przemysłowej doświadczyła wielu innowacji technologicznych, które mają na celu zwiększenie efektywności procesów oraz poprawę jakości produktów. Jednym z najważniejszych trendów jest automatyzacja procesów destylacyjnych, która pozwala na precyzyjne monitorowanie i kontrolowanie parametrów pracy urządzeń. Dzięki zastosowaniu nowoczesnych czujników i systemów sterowania możliwe jest szybkie reagowanie na zmiany warunków pracy oraz optymalizacja procesów w czasie rzeczywistym. Kolejną innowacją jest rozwój materiałów używanych do budowy kolumn i zbiorników destylacyjnych, które charakteryzują się lepszą odpornością na korozję oraz wyższą efektywnością wymiany ciepła. Ponadto coraz częściej stosuje się technologie odzysku ciepła, które pozwalają na zmniejszenie zużycia energii podczas procesów destylacyjnych.
Jakie są wymagania dotyczące bezpieczeństwa w użytkowaniu destylatorów przemysłowych
Bezpieczeństwo użytkowania destylatorów przemysłowych jest niezwykle istotnym aspektem, który należy brać pod uwagę na każdym etapie ich eksploatacji. Przemysłowe procesy destylacyjne często wiążą się z wysokimi temperaturami oraz ciśnieniem, co stwarza ryzyko wystąpienia awarii lub zagrożeń dla zdrowia pracowników. Dlatego też konieczne jest przestrzeganie rygorystycznych norm bezpieczeństwa oraz regulacji prawnych dotyczących użytkowania tego typu urządzeń. Wymagania te obejmują m.in. regularne przeglądy techniczne, konserwację sprzętu oraz szkolenie pracowników w zakresie obsługi i bezpieczeństwa pracy. Ważne jest również wyposażenie zakładów w odpowiednie systemy zabezpieczeń, takie jak czujniki gazu czy automatyczne wyłączniki awaryjne.
Jakie są przyszłe kierunki rozwoju technologii destylacji przemysłowej
Przyszłość technologii destylacji przemysłowej zapowiada się obiecująco dzięki ciągłemu postępowi technologicznemu oraz rosnącym wymaganiom rynkowym. Wśród kluczowych kierunków rozwoju można wymienić dalszą automatyzację procesów produkcyjnych, co pozwoli na zwiększenie efektywności i redukcję kosztów operacyjnych. Technologie sztucznej inteligencji i uczenia maszynowego będą miały coraz większy wpływ na optymalizację procesów destylacyjnych poprzez analizę danych i prognozowanie wydajności produkcji. Ponadto rośnie zainteresowanie ekologicznymi rozwiązaniami, takimi jak odzysk ciepła czy wykorzystanie odnawialnych źródeł energii w procesach produkcyjnych. W miarę jak przedsiębiorstwa będą dążyć do zmniejszenia swojego śladu węglowego, innowacje te staną się kluczowe dla przyszłości branży destylacyjnej.
Jakie są różnice między destylacją a innymi metodami separacji
Destylacja to jedna z wielu metod separacji składników mieszanin chemicznych, jednak różni się od innych technik pod względem zasady działania oraz zastosowań. W przeciwieństwie do filtracji czy ekstrakcji, które opierają się na różnicach w wielkości cząsteczek lub rozpuszczalności substancji, destylacja wykorzystuje różnice w temperaturze wrzenia składników mieszaniny. Dzięki temu możliwe jest oddzielanie substancji o różnych właściwościach fizycznych bez konieczności stosowania rozpuszczalników czy innych chemikaliów pomocniczych. Destylacja jest szczególnie skuteczna w przypadku cieczy i gazów, natomiast inne metody separacji mogą być bardziej odpowiednie dla substancji stałych lub emulsji.
Jakie są najważniejsze czynniki wpływające na wydajność destylatora przemysłowego
Wydajność destylatora przemysłowego zależy od wielu czynników, które mają kluczowy wpływ na efektywność procesu separacji składników mieszanin chemicznych. Jednym z najważniejszych czynników jest temperatura podgrzewania cieczy; jej odpowiednie ustawienie pozwala na optymalne parowanie składników o niższej temperaturze wrzenia. Również konstrukcja kolumny destylacyjnej ma znaczenie; wysokość kolumny oraz liczba poziomych przekładek wpływają na ilość kontaktu pary z cieczą skraplaną, co zwiększa efektywność separacji. Inne istotne czynniki to ciśnienie wewnętrzne w systemie oraz czas trwania procesu; ich optymalizacja pozwala na uzyskanie lepszych wyników w krótszym czasie.